Taizhou Fupusi Machinery Co., Ltd. is a company that produces semi-auto blow machines, full auto blow machines, and molds, it can make plastic bottles and containers for mineral water, edible oil, soda, wine, cosmetics, lotion, detergent, pharmaceuticals, pesticides, food cans, daily chemicals, hot filling beverages, and other fields industries. plastic extrusion blowing machine
Daily maintenance is the basis for maintaining smooth operation of the machine, which can be learned by the operator observing the condition when the machine is running.
In daily observation, pay attention to the operation of the machine and some conversion actions of feeding and removing bottles, etc. When some minor problems are found, stop the operation immediately and solve them quickly to reduce some unnecessary losses.
Taizhou Fupusi Machinery Co., Ltd Daily maintenance work is almost always carried out when the machine is running, including checking all adjustable data such as mold closing time, delayed blowing time, pre-blowing time, bottle blowing time, etc. plastic hdpe/ldpe blow molding machine
Daily maintenance is not static, it depends on the operation and environmental conditions of the machine.
Therefore, to make the machine run smoothly, when the bottle inventory is sufficient or the machine stop time is appropriate, a thorough inspection will be more conducive to the operation of the machine.
The operator should pay attention to whether the oil level of the air compressor lubricating oil is sufficient.plastic bottle making machine
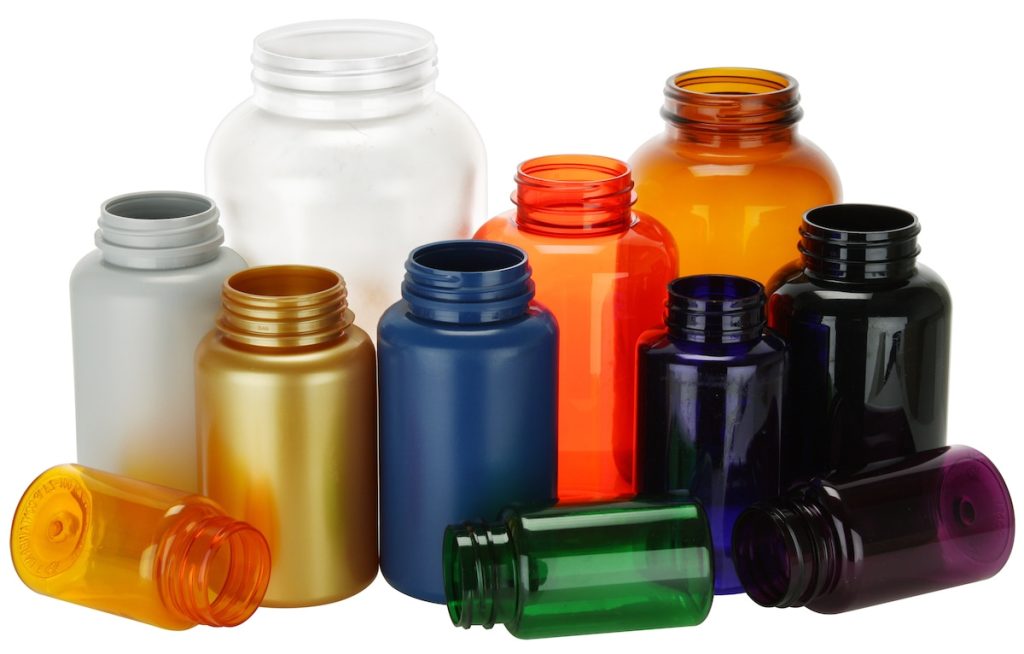
Cleaning
Keeping the machine clean in daily maintenance will help the machine run smoothly. When wiping excess grease on the machine, especially when wiping excess grease on the connecting rod of the mold closing mechanism, the machine must be stopped. hand feeding automatic blow molding machine pet bottle blower pet blow moulding machine
Check whether the screws of each part are loose, whether the position fixing nuts of each group of proximity switches are loose, and whether the conveyor belt of the feeder is too loose.
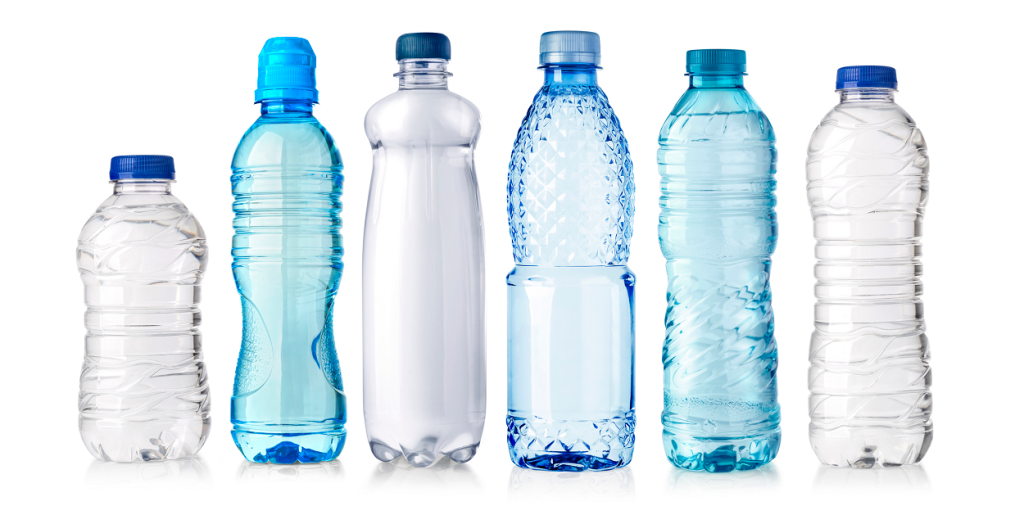
Taizhou Fupusi Machinery Co., Ltd Daily inspection and maintenance items:
⑴ Check the quality of the bottle.
⑵ Whether the circulating water is blocked
⑶ Listen to whether the machine has abnormal sounds and whether the pipeline is leaking
⑷ Check whether the fixing nuts of each solenoid valve coil are loose
⑸ Check whether each pipeline is bent
⑹ Discharge the drain valve of the air storage cylinder and related equipment (please drain every four hours in places with high humidity)
⑺ Check whether the operating circuit and high-pressure blowing pressure are normal
⑻ Check whether the tension dry fixing bolts and fiber screws are loose
⑼ Check the bottom drive travel nut
⑽ Check whether the oil mist is sufficient, whether the oil of the motor speed gearbox is sufficient, and the lubricating oil is L-DAB150 in summer and L-DAB100 in winter.
⑾ Is the exhaust fan normal?
⑿ Check the air compressor lubricating oil once a day
blow molding machine, blow moulding machine blowing machine
Taizhou Fupusi Machinery Co., Ltd –
there are two types of blow molding machine for Pet in the market
the first one is semi automatic blow molding machine, this one machine cost and production capacity is low , it mainly decide by the worker operating , simply speaking, the pet preform is heated by the heater , then shaped under blow mold
The second is fully automatic blow molding machine
it’s cost and production capacity is high
For PET Preform Mould
Number of machines and ancillary machines are required to get best quality PET preform
Below we have consider few of them to help you have picture of machines and their best use.
Practically I have shared picture of machines that MG Moulds Systems Pvt Ltd company use to manufacture best PET preform moulds for best PET preforms.
CNC machines are like the wizards of precision manufacturing for PET preform moulds. Picture them as incredibly skilled sculptors, but instead of chisels and hammers, they use advanced computer-controlled tools. These machines come in different Types like milling machines, lathes, and machining centres, each with its unique specialty. Think of CNC milling machines as the artists who carve intricate designs into blocks of metal, creating the detailed shapes needed for PET preform moulds. They follow precise instructions from computer programs, ensuring every cut is spot-on.Then there are CNC lathes, which are like the master craftsmen turning cylindrical pieces of metal into perfectly shaped components for the moulds. They spin the material while cutting it with precision, forming smooth curves and precise dimensions.Machining centres are the multitaskers of the CNC world, capable of performing various operations like milling, drilling, and tapping all in one go. They’re like the Swiss Army knives of mould-making, efficiently shaping different parts of the mould with finesse.These CNC machines work with materials like aluminium or steel, transforming them into the backbone of PET preform moulds. Their precision and accuracy ensure that every mould produced is of top-notch quality, ready to churn out flawless PET preforms.
According to whether the nozzle is retracted before and after the pre-plastic feeding, that is, whether the nozzle leaves the mold, the injection molding machine generally has three options. Fixed feeding: the nozzles are always stuck into the mold before and after pre-molding, and the nozzle does not move.
Pre-feeding: The nozzle is pre-plasticized with the mold, the pre-molding is completed, the nozzle is retracted, and the nozzle leaves the mold. The purpose of this method is to use the mold injection hole to assist the nozzle during the pre-molding to avoid the melt flowing out of the nozzle when the back pressure is high. After the pre-molding, the nozzle and the mold can be prevented from contacting for a long time to generate heat transfer, affecting them. The respective temperatures are relatively stable.
If i m getting ur question right then you wanna know WHICH machine can make the pet preform MOULD better
Taizhou Fupusi Machinery Co., Ltd -For manufacturing of mould you can always go with sparking machine such as charmills, makino or sodick these machines with proper grade alloy electrodes ensures accuracy upto 2–5 microns, which is more than required accuracy, as it is just a intermediate product.
Furthermore the mould requires proper injection moulding machine that can ensure 100% utilisation of mould capacity.
The top rated champions in injection moulding machines for pet are HUSKY and NETSTAL injection moulding machines, these machines deliver extraordinarily performances.
If one is intrested then these injection moulding machine manufacturers can suggest you the best mouldmaker and beat suited subsidary accessories alongside.
Maintaining a bottle blowing machine is essential for ensuring optimal performance, longevity, and product quality. Here’s a general guide on how to maintain such a machine:
1. Regular Cleaning
- Daily Cleaning: Clean the machine at the end of each production day. Remove any plastic residue and dust.
- Weekly Cleaning: Perform a more thorough cleaning, including the molds, heating elements, and air filters.
- Use Appropriate Cleaners: Use non-corrosive and non-abrasive cleaning agents suitable for the materials of the machine.
2. Lubrication
- Check Lubrication Points: Regularly check and lubricate moving parts as specified in the manufacturer’s manual.
- Use Recommended Lubricants: Use lubricants recommended by the manufacturer to avoid damage.
3. Inspection of Components
- Molds: Regularly inspect molds for wear and tear. Replace any damaged molds to ensure quality production.
- Heating Elements: Check heating elements for functionality and cleanliness. Replace any faulty components.
- Cooling System: Ensure the cooling system is operational and free of blockages.
4. Air Supply Maintenance
- Check Air Compressors: Ensure that air compressors are functioning properly and that filters are clean.
- Monitor Air Pressure: Regularly check and adjust air pressure settings according to production requirements.
5. Electrical Components
- Inspect Wiring: Regularly check all electrical connections and wiring for signs of wear or damage.
- Test Safety Features: Ensure all safety features, such as emergency stops and sensors, are operational.
6. Calibration
- Regular Calibration: Periodically calibrate the machine to ensure accurate measurements and settings for bottle dimensions.
- Follow Manufacturer Guidelines: Adhere to the calibration schedule recommended by the manufacturer.
7. Documentation
- Maintenance Log: Keep a detailed log of all maintenance activities, including inspections, repairs, and parts replacements.
- Follow Manufacturer’s Manual: Always refer to the machine’s manual for specific maintenance procedures and schedules.
8. Training and Safety
- Train Operators: Ensure that all operators are properly trained in machine operation and maintenance.
- Safety Protocols: Follow all safety protocols to minimize risks during operation and maintenance.
Conclusion
Regular maintenance of a bottle blowing machine can significantly enhance its performance, reduce downtime, and prolong its lifespan. Always refer to the specific manufacturer’s guidelines for detailed maintenance procedures tailored to your machine model.
Blow molding machine plastic extrusion machine pet blowing machine