The blow molding process is a bidirectional stretching process, during which the PET chain is bidirectionally extended, oriented and arranged, thereby increasing the mechanical properties of the bottle wall, improving the tensile, tensile and impact strength, and having good air tightness. Although stretching helps to improve strength, it cannot be overstretched, and the stretch-blow ratio must be controlled; the radial direction should not exceed 3.5-4.2, and the axial direction should not exceed 2.8-3.1. The wall thickness of the preform should not exceed 4.5mm.
The fully automatic wide-mouth dynamic blow molding machine is carried out between the glass transition temperature and the crystallization temperature, which is generally controlled between 90-120 degrees. In this range, PET is rapidly blown in a high elastic state, and becomes a transparent bottle after cooling and shaping. In the one-step method, this temperature is determined by the cooling time during the injection molding process, so the relationship between the injection-blowing two stations must be connected.
The blow molding process includes: stretching-one blow-two blows, and the time of the three actions is very short, but they must be well coordinated, especially the first two steps determine the overall distribution of the material and the quality of the blow molding machine. Therefore, it is necessary to adjust the stretching start timing, stretching speed, pre-blowing start and end timing, pre-blowing pressure and pre-blowing flow rate, etc. If possible, it is best to control the overall temperature distribution of the preform and the temperature gradient of the inner and outer walls of the preform.
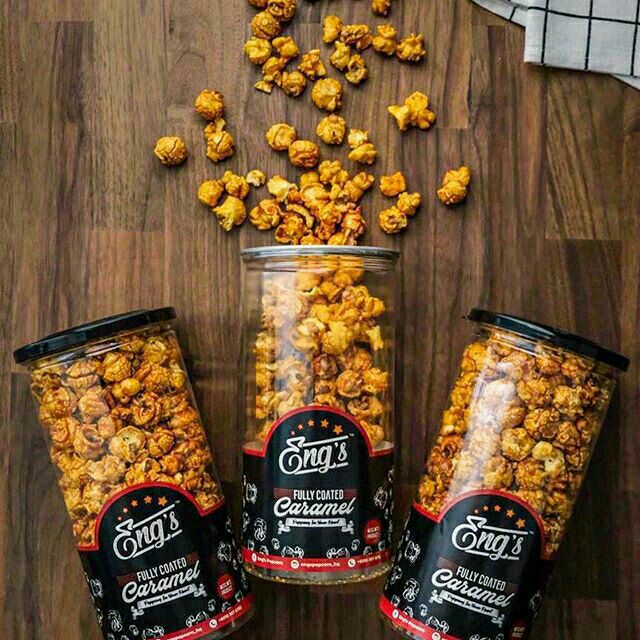
Common problems and solutions for induced stress in the bottle wall of the fully automatic wide-mouth dynamic blow molding machine during rapid blow molding and cooling:
- Thick on the top and thin on the bottom: delay the pre-blowing time or reduce the pre-blowing pressure to reduce the air flow.
- Thick on the bottom and thin on the top: the opposite of the above.
- There are wrinkles under the bottleneck: the pre-blowing is too late or the pre-blowing pressure is too low, or the preform is not cooled well here.
- The bottom is white: the preform is too cold, over-stretched, pre-blowing too early or the pre-blowing pressure is too high.
- There is a magnifying glass phenomenon at the bottom of the bottle: too much material at the bottom of the bottle, pre-blowing too late, and pre-blowing pressure is too low.
- There are wrinkles inside the bottom of the bottle: the bottom temperature is too high, the cooling at the gate is not good, the pre-blowing is too late, the pre-blowing pressure is too low, and the flow rate is too small.
- The whole bottle is turbid: opaque, insufficient cooling.
- Partial whitening: excessive stretching, the temperature here is too low, or the pre-blowing is too early, or the stretching rod is touched.
- Bottle bottom eccentricity: It may be related to preform temperature, stretching, pre-blowing, high-pressure blowing, etc. Reduce the preform temperature, speed up the stretching speed, check the gap between the tie rod head and the bottom mold, delay pre-blowing, reduce pre-blowing pressure, delay high-pressure blowing, and check whether the preform is eccentric.